РЕМОНТ РУЛЕВОГО МЕХАНИЗМА С ВСТРОЕННЫМ ГИДРОУСИЛИТЕЛЕМ.
Ремонт, обслуживание и устройство, ремонт рулевого механизма с встроенным гидроусилителем автомобиля КАМАЗ.
Рулевой механизм (рис. 7.6) закрепляют в тисках и устанавливают вал 10 сошки в среднее положение. Отвернув гайку и болты с шайбами крепления боковой крышки 27, снимают боковую крышку в сборе с валом 10 сошки. Придерживая вал 10, вывертывают винт 25, снимают крышку 27 и извлекают из нее манжету и уплотнительные кольца. Специальными пассатижами И-801.23.000 снимают стопорное кольцо 28, а затем — шайбы 29, 30 и уплотнительное кольцо.
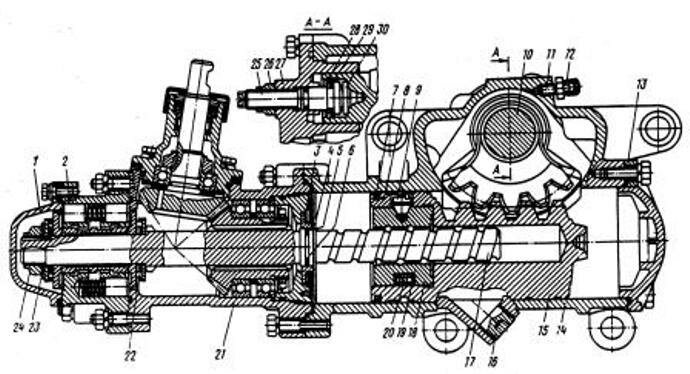
Рис. 7.6. Рулевой механизм с встроенным гидроусилителем:
1 — крышка передняя; 2 — клапан управления гидроусилителем; 3. 28 — кольца стопорные; 4 — втулка плавающая; 5, 7 — кольца уплотнительные; 6, 8 — кольца распорные; 9 — винт установочный; 10 — вал сошки; 11 — клапан перепускной; 12 — колпачок защитный; 13 — крышка задняя; 14 — картер рулевого механизма; 15 — поршень; 16 — пробка сливная магнитная; 17 — винт; 18 — гайка шариковая; 19 — желоб; 20 — шарик; 21 — редуктор угловой; 22 — роликоподшипник упорный; 23 — шайба пружинная; 24, 26 — гайки; 25 — винт регулировочный; 27 — крышка боковая; 29 — шайба регулировочная; 30 — шайба упорная
Вывернув и сняв болты с шайбами крепления передней крышки 1, снимают крышку и уплотнительное кольцо. Затем следует зафиксировать от поворота вал ведущей шестерни углового редуктора во избежание высыпания шариков 20 из шариковой гайки 18 и заклинивания винта 17, а также поломки усов шайбы 23 и повреждения резьбы винта 17 при отвертывании гайки 24. Отвернув гайку 24, снимают шайбу 23 и первый подшипник 22, вывертывают и снимают болты и гайки с шайбами крепления клапана 2 управления гидроусилителя. При этом необходимо предохранить от выпадания реактивные плунжеры 8 (рис. 7.7) клапана управления.
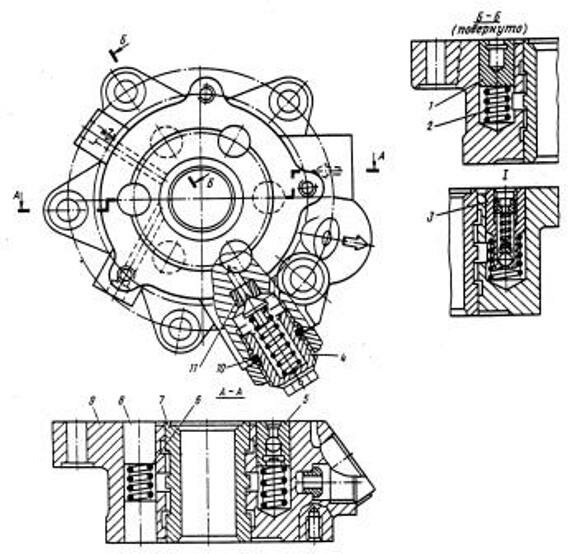
Рис. 7.7. Клапан управления гидроусилителем рулевого управления:
1 — плунжер; 2. 6 —- пружины; 3, 11 — клапаны предохранительные; 4 — винт регулировочный; 5 — клапан обратный; 7 — золотник; 8 — плунжер реактивный; 9 — корпус клапана; 10 — кольцо уплотнительное
С винта 17 (см. рис. 7.6) снимают клапан 2 управления в сборе и второй подшипник 22. Из каналов высокого давления редуктора 21 извлекают уплотнительные кольца. Вывернув и сняв болты и гайки с шайбами крепления углового редуктора 21, снимают угловой редуктор в сборе с винтом 17 и поршнем-рейкой 15.
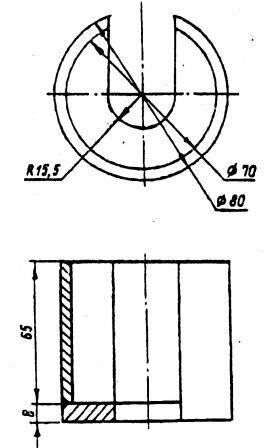
Рис. 7.8. Приспособление для выпрессовки шариковой гайки и вывертывания установочных винтов
Из углового редуктора, сняв распорное кольцо, вынимают винт 17 с поршнем-рейкой 15 и устанавливают их в тиски. С помощью приспособления, изображенного на рис. 7.8, вывертывают установочные винты 9 (см. рис. 7.6) и выпрессовывают шариковую гайку 18, а затем вывертывают из поршня 15 винт 17, удерживая от выпадения желобки 19. Вынув желобки 19 и вывертывая винт 17, высыпают шарики 20 (всего 31 шарик) в тару, куда укладывают также винт и шариковую гайку, поместив их и тару одинаковыми метками во избежание разукомплектования. Затем снимают плавающую втулку 4, уплотнительное 5 и стопорное 3 кольца.
Из картера 14 вывертывают сливную пробку 16 и перепускной клапан 11 в сборе, извлекают упорное кольцо, манжеты и выпрессовывают втулку. Вывернув болты с шайбами крепления задней крышки 13, снимают заднюю крышку с уплотнительным кольцом.
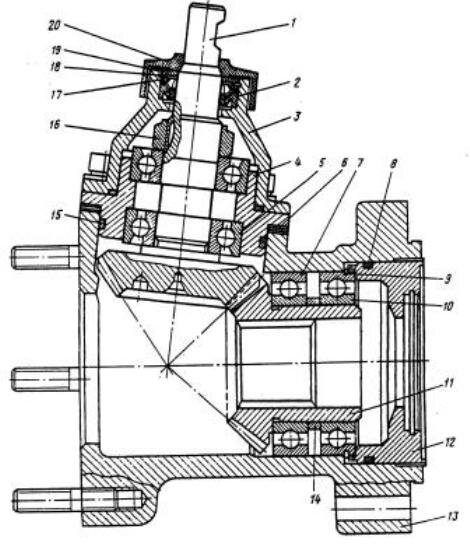
Рис. 7.9. Редуктор угловой:
1 — шествия ведущая; 2 — манжета; 3 — крышка корпуса; 4 — корпус ведущей шестерни; 5, 7, 10 — шарикоподшипники; 6 — прокладки регулировочные; 8. 15, 19 — кольца уплотнительные; 9 — кольцо стопорное; 11 — шестерня ведомая; 12 — крышка упорная; 13 — корпус редуктора; 14 — втулка распорная; 16 — гайка крепления подшипников; 17 — шайба; 18 — кольцо упорное; 20 — колпачок защитный
Закрепив угловой редуктор в тисках, вывертывают болты с шайбами крепления крышки 3 корпуса ведущей шестерни (рис. 7.9), снимают защитный колпачок 20 и крышку 3. Вынув уплотнительное 19 и упорное 18 кольца, шайбу 17 и манжету 2, снимают ведущую шестерню 1 с корпусом 4 в сборе.
Отвернув гайку 16, снимают уплотнительное кольцо 15 и вынимают из корпуса 4 шестерню 1 с подшипником 5. Из корпуса 4 выпрессовывают второй подшипник. С вала шестерни съемником спрессовывают подшипник 5.
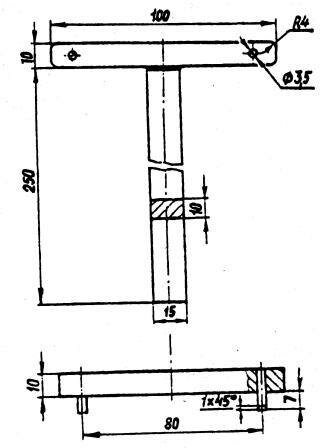
Рис. 7.10. Ключ для отвертывания упорной крышки.
Вывернув упорную крышку 12 с помощью специального ключа (рис. 7.10), снимают уплотнительное кольцо 8 (см. рис. 7.9), выпрессовывают ведомую шестерню 11 в сборе с подшипниками и снимают упорное кольцо. С помощью съемника спрессовывают подшипники 7 и 10 с вала шестерни. Ведущую 1 и ведомую 11 шестерни не разукомплектовывают.
Из корпуса 9 (см. рис. 7.7) клапана управления извлекают реактивные плунжеры 1, 8, обратный клапан 5, реактивные пружины 2, 6 и золотник 7 клапана управления. Реактивные плунжеры и золотник подобраны к отверстиям в корпусе клапана и не разукомплектовываются, для чего их необходимо пометить. Отвернув гайку, вывертывают регулировочный винт 4 так, чтобы не выпали игла и пружина, после чего вынимают эти детали и снимают уплотнительное кольцо 10. Обратный клапан 5 разбирают, если это необходимо для очистки или замены деталей. Разогнув и вынув шплинт, извлекают шарик.
Снятые детали рулевого механизма моют, обдувают сжатым воздухом и дефектуют.
Игольчатые подшипники бракуют при видимом износе игл и наличии ямок — следов от вдавливания игл на рабочих поверхностях колец.
Шарикоподшипники бракуют при затрудненном поворачивании колец и при осевом зазоре, определяемом щупом, более 0,3 мм.
Картер рулевого механизма бракуют при наличии трещин, обломов, заметном короблении, при износе отверстий под поршень-рейку до диаметра более 105,05 мм и втулки до диаметра более 58,04 мм. Отдельные задиры на зеркале цилиндра устраняют механической обработкой.
Поршень-рейку бракуют при наличии трещин, обломов, выкрашивании или раковинах на рабочих поверхностях зубьев, при износе поршня по наружному диаметру до размера менее 104 мм и канавки до диаметра менее 93,45 мм. Изношенную или сорванную резьбу восстанавливают.
Вал сошки бракуют при наличии трещин, обломов, выкрашивании, раковинах на рабочих поверхностях зубьев или их заметном износе, при износе, срезе или скручивании шлицев, износе вала по наружному диаметру до размера менее 57,92 мм и канавки под уплотнительное кольцо до ширины более 1,85 мм.
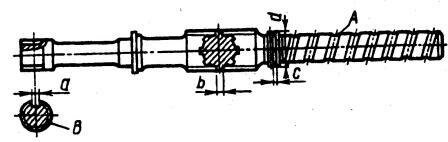
Рис. 7.11. Винт рулевого управления
Винт рулевого управления бракуют при наличии трещин или обломов, вмятин от шариков и задиров на поверхности А (рис. 7.11), а также при износе: шлицев по ширине — до размера b менее 5,95 мм; канавки для уплотнительного кольца — до ширины С более 2,5 мм; шейки — до наружного диаметра d менее 29,9 мм; канавки — до ширины а более 5,5 мм.
Изношенную или сорванную резьбу В восстанавливают.
Корпус углового редуктора бракуют при наличии трещин и обломов, при износе отверстия под подшипник ведущей шестерни до диаметра более 80,05 мм. Изношенную или сорванную резьбу восстанавливают.
Шестерню ведущую бракуют при наличии трещин, обломов, выкрашивании, раковинах на рабочих поверхностях зубьев или их заметном износе, при износе или скручивании шлицев, износе шеек вала по наружному диаметру до размера большей шейки менее 25,0 мм и меньшей — 21,97 мм.
Шестерню ведомую бракуют при наличии трещин, обломов, выкрашивании, раковинах или заметном износе на рабочих поверхностях зубьев, при износе вала по наружному диаметру до размера менее 50,007 мм и износе впадин шлицев до ширины более 6,08 мм.
Гайку упорную бракуют при наличии трещин и обломов, выкрашивании и рисках на поверхности, при ширине канавки более 2,3 мм. При износе или срыве более одной нитки резьбы резьбу восстанавливают.
Втулку плавающую бракуют при наличии трещин, обломов, заметном износе или выкрашивании рабочих поверхностей, износе отверстия до диаметра более 30,043 мм.
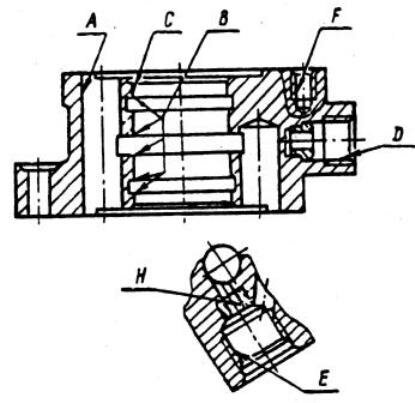
Рис. 7.12. Корпус клапана управления гидроусилителем 220
Корпус клапана управления гидроусилителем бракуют при наличии трещин и обломов, рисках и задирах на поверхностях A, С (рис. 7.12), при разрушении кромок В. При забоинах или овальности поверхности Н заменяют седло клапана. При износе или срыве резьб F, D, Е резьбу восстанавливают.
Золотник клапана управления гидроусилителем бракуют при наличии трещин и обломов, рисках и задирах на наружной поверхности.
Иглу предохранительного клапана бракуют при обломах или погнутости иглы, вкрапливании инородных частиц или неравномерном износе конусной поверхности.
При сборке рулевого механизма в корпус обратного клапана 5 (см. рис. 7.7) вкладывают шарик и устанавливают шплинт. Концы шплинта загибают в кольцевую канавку корпуса заподлицо с наружной поверхностью. Не допускаются выступание отогнутых концов шплинта и его повторное использование.
В корпус 9 клапана управления вставляют золотник 7 проточкой в сторону углового редуктора. Перемещение золотника должно быть плавным, без заеданий. В глухие отверстия клапана управления устанавливают пружины 2, плунжеры 1 и обратный клапан 5. В сквозные отверстия вставляют по два плунжера 8 с пружинами 6. Плунжеры должны быть установлены фасками наружу согласно меткам, сделанным при разборке, и перемещаться плавно, без заеданий.
На регулировочный винт 4 надевают уплотнительное кольцо 10. Вложив в гнездо корпуса клапана иглу и пружину, ввертывают регулировочный винт и навертывают гайку.
На ведомую шестерню 11 (см. рис. 7.9) напрессовывают подшипник 7, устанавливают втулку 14, напрессовывают подшипник 10 проточкой на наружной обойме наружу и устанавливают в проточку упорное кольцо. Ведомую шестерню в сборе устанавливают в корпус редуктора. На упорную крышку 12 устанавливают уплотнительное кольцо 8, ввертывают крышку в корпус редуктора до упора и стопорят ее, вдавив кромку буртика корпуса редуктора в прорезь крышки. В корпус 4 ведущей шестерни запрессовывают подшипник 5. На шестерню 1 напрессовывают второй подшипник 5, запрессовывают их в корпус 4 и устанавливают уплотнительное кольцо 15. Завернув гайку 16, проверяют легкость вращения шестерни и отсутствие ее осевого перемещения, после чего вдавливают буртик гайки в паз вала шестерни. В крышку 3 корпуса ведущей шестерни запрессовывают манжету 2, устанавливают шайбу 17 и упорное кольцо 18.
На верхний фланец корпуса 13 редуктора устанавливают прокладки 6, ведущую шестерню 1 в сборе, крышку 3 корпуса ведущей шестерни в сборе, регулируют зацепление шестерен 1 и 11.
Боковой зазор в зацеплении шестерен регулируют подбором прокладок 6, при этом допускается устанавливать прокладки толщиной 0,05 мм не менее трех штук. Боковой зазор между любой парой зубьев должен быть не более 0,1 мм. Пятно контакта должно находиться в средней части зуба. Момент поворота ведущей шестерни не должен превышать 49 Н*см (5 кгс*см). Отрегулировав зацепление шестерен, закрепляют крышку 3 болтами с шайбами, устанавливают уплотнительное кольцо 19 и защитный колпачок 20.
Запрессовав в картер 14 (см. рис. 7.6) втулку и манжеты, устанавливают упорное кольцо. Установив в картер с противоположной стороны шайбу, запрессовывают манжету и вкладывают в проточку крышки 13 уплотнительное кольцо. На винт 17 устанавливают стопорное 6 и уплотнительное 5 кольца, втулку 4, стопорное кольцо 3 и шариковую гайку 18. Втулку устанавливают плоской стороной к шлицам винта, шариковую гайку — фаской в сторону винтовой канавки. Внутреннюю поверхность желобов 19 покрывают тонким слоем смазки Литол-24, устанавливают шарики 20 (восемь штук) в один желоб, накрывают его вторым желобом и замазывают выход из желобов смазкой Литол-24 для предотвращения выпадания шариков.
Медленно вращая винт 17 против часовой стрелки, вталкивают 23 шарика через обращенное к буртику винта отверстие в гайке 18. Желобы с шариками устанавливают в пазы гайки и обвязывают гайку бечевкой. В средней части винта гайка должна поворачиваться плавно под действием момента 29,4...78,5 Н* м (3...8 кгс*м), а по краям — свободно. Для увеличения момента сопротивления повороту шарики заменяют на другие, с большим диаметром. Не допускается использовать шарики, у которых разность диаметров более 0,002 мм.
На поршень 15 устанавливают распорное 8 и уплотнительное 7 кольца. На шариковую гайку, сняв бечевку, надевают поршень 15 и ввертывают установочные винты 9, затянув их с моментом 49,0...58,9 Н*м (5...6 кгс*м). Если прорезь в головке винта расположится вдоль проточки на поршне, винт необходимо заменить на новый. Выступание винта или выступов от кернения над цилиндрической поверхностью поршня недопустимо. Винты стопорят, вдавив их края в двух местах в проточку поршня. Поршень предохраняют от проворачивания относительно винта 17 во избежание высыпания шариков. В корпус углового редуктора устанавливают винт 17 в сборе с поршнем 15 и, прижав плавающую втулку 4 к упорной гайке, устанавливают в канавку гайки кольцо.
В каналы высокого и низкого давлений переднего фланца картера 14 устанавливают уплотнительные кольца, поршень 15 в сборе с угловым редуктором 21 и скрепляют их болтами и гайками с пружинными шайбами [момент затяжки 34,3...41,2 Н*м (3,5...4,2 кгс*м)]. На выступающий из корпуса углового редуктора конец винта 17 напрессовывают подшипник 22, устанавливают в канавку на переднем торце корпуса редуктора и в каналы высокого давления уплотнительные кольца, устанавливают клапан 2 управления в сборе и наружный подшипник 22. Затем устанавливают пружинную шайбу 23 вогнутой стороной к подшипнику и, удерживая от поворота ведущую шестерню, завертывают гайку 24 до тех пор, пока не будет достигнут момент поворота клапана управления относительно винта 98,1...122,6 Н*см (10,0...12,5 кгс*см), после чего вдавливают край гайки в паз винта. Гайки и болт крепления клапана управления затягивают с моментом 34,3.41,2 Н*м (3,5...4,2 кгс*м). Установив крышку 1 с уплотнительным кольцом, закрепляют их болтами с шайбами [момент затяжки 20,6...27,5 Н*м (2,1...2,8 кгс*м)].
В вал 10 сошки устанавливают упорную шайбу 30, винт 25 с предварительно надетым на него уплотнительным кольцом, регулировочную шайбу 29 и стопорное кольцо 28. Подбором регулировочной шайбы 29 по толщине добиваются осевого перемещения вала сошки относительно регулировочного винта в пределах 0,02...0,08 мм. В боковую крышку 27 запрессовывают манжету и устанавливают в канал низкого давления уплотнительное кольцо. На винт 25 навертывают до упора боковую крышку 27 в сборе и гайку 26, в канaвки боковой крышки устанавливают уплотнительное кольцо.
Установив поршень 15 в среднее положение, вставляют в картер 14 боковую крышку 27 в сборе с валом 10 сошки так, чтобы не повредить манжеты и чтобы средний зуб сектора вала сошки вошел во вторую впадину поршня, после чего закрепляют крышку болтами с шайбами.
Установив заднюю крышку 13, закрепляют ее болтами с шайбами, ввертывают перепускной клапан 11 в сборе и магнитную пробку 16 [момент затяжки 29,4...39,2 Н*м (3...4 кгс*м)]. Боковой зазор в зацеплении рейка — сектор регулируют вращением регулировочного винта 25. Момент сопротивления вращению ведущей шестерни при ее переходе через среднее положение должен быть в пределах 2,9...5,4 Н*м (0,30... 0,55 кгс*м), а после поворота в любую сторону от среднего положения более чем на два оборота — 1,5...2,9 Н*м (0,15...0,3 кгс*м). После регулировки, удерживая регулировочный винт, затягивают гайку 26 [момент затяжки 56,9...64,7 Н*м (5,8...6,6 кгс*м)].
После сборки рулевой механизм испытывают на стенде, оборудованном насосом подачей не менее 9 л/мин и обеспечивающем подвод масла марки Р при температуре не ниже 40 С к отверстию корпуса клапана управления гидроусилителем. Удалив воздух из системы, регулируют предохранительный клапан стендового насоса на давление открытия 5,4 МПа (55 кгс/см ) и проверяют следующее:
вращение ведущей шестерни в любую сторону при моментах сопротивления вращению вала сошки 0 и 1,28 кН • м (130 кгс • м) должно быть плавным и без заеданий;
давление на входе в клапан управления гидроусилителем при нейтральном положении золотника должно быть не более 294 кПа (3 кгс/см 2);
утечка на выходе из клапана управления гидроусилителем при повороте ведущей шестерни вправо или влево до упора не должна превышать 1500 см3/мин (начало измерения через 5 с после поворота, время измерения — не более 20 с);
поворот вала сошки из одного крайнего положения в другое должен происходить при приложении момента не более 117,7 Н • м (12 кгс • м).
Отрегулировав предохранительный клапан стендового насоса на давление открытия 8,8 МПа (90 кгс/см ), проверяют следующее:
предохранительный клапан рулевого механизма должен открываться при давлении 7,36 ... 7,85 МПа (75... 80 кгс/см ), что регулируется вращением винта 25 (см. рис. 7.6), после чего необходимо затянуть гайку 26 с моментом 39,2...58,9 Н*м (4...6 кгс*м); возможный при работе клапана шум не является браковочным признаком;
давление в нагнетательной магистрали, при повороте ведущей шестерни вправо и влево до упора должно быть 7,36...7,85 МПа (75...80 кгс/см2), а после снятия усилия с винта без притормаживания и остановки вала ведущей шестерни должно быстро падать до значения не более 294 кПа (3 кгс/см2 );
при давлении 8,8 МПа (90 кгс/см2), обеспечиваемом клапаном на возвратной линии, подтекание масла не допускается (герметичность рулевого механизма проверяют в течение 5 мин в обоих крайних положениях поршня);
свободный ход (угол поворота) вала ведущей шестерни до повышения давления в напорной магистрали на 78,5 кПа (0,8 кгс/см 2) должен быть 3... 5° в каждую сторону, а суммарный свободный ход влево и вправо — не более 10 ° .
После испытания рулевого механизма устанавливают чехол предохранительного клапана и пломбируют клапан, пропустив проволоку через чехол, регулировочный винт и отверстие в ушке корпуса клапана управления.
Ремонт, обслуживание и устройство, ремонт рулевого механизма с встроенным гидроусилителем автомобиля КАМАЗ.